We don’t realize it, but hydrogen is becoming increasingly important in many countries. Many governments have realized that it is the key to an efficient and environmentally friendly future.
But… why exactly?
Clean or green hydrogen has evolved into a promising market due to the private sector’s current political climate and interest. Most governments and private companies are exploring hydrogen capabilities, and there is a chance that hydrogen will become the energy (carrier) of the future. This would mean new plants, fueling stations, vehicles, and, luckily for us; it will require valves to make it happen.
What is hydrogen used for?
That would be the first question that needs to be asked.
So… a quick explanation:
Hydrogen is currently used mainly for industrial purposes such as oil refining, ammonia-, methanol- and steel production. Most valve manufacturers have developed and marketed their valves for hydrogen use since it’s not infrequent to find them in several industrial processes. However, for hydrogen to become an essential part of clean and secure energy, it needs to be adopted in other sectors such as transport, buildings, and power generation.
Fortunately, new developments are being achieved to find new applications in those sectors. These include:
- buses for public transport, trains and ships (large scale transport)
- personal vehicles
- backup power generation for hospitals and data centers using uninterruptible power supply (UPS) systems
- mobile power generation
- substituting natural gas in multi-family and commercial buildings
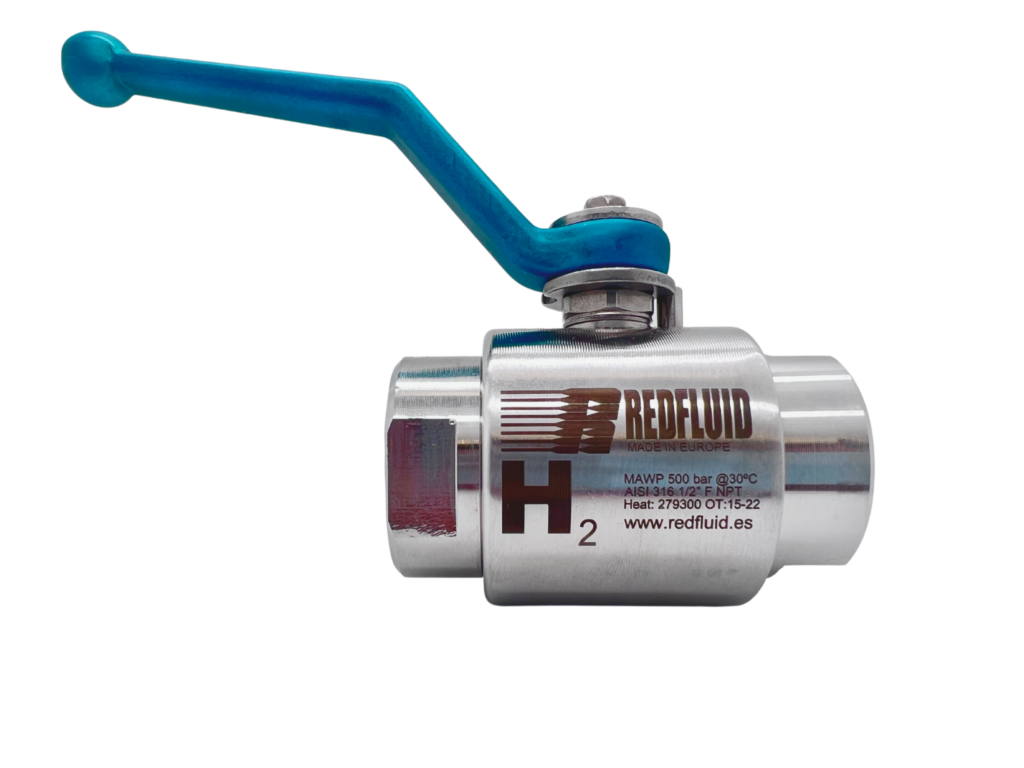
What challenges do we face using hydrogen?
Everything sounded perfect, but there are always some challenges that we should consider. The most relevant are:
- hydrogen is currently produced from fossil fuels because it is still costly to produce based on renewable energy
- hydrogen infrastructure is being developed slowly
- extreme conditions to store and to dispense with extremely high pressures and low (cryogenic) temperatures
- controlling the flow of minuscule hydrogen molecules without leakage
Hydrogen Production Test for Ball Valve
Here’s a practical video where I explain what a production test is. Plus, I perform the test using our 3-piece hydrogen ball valve rated up to 250 bar. Pretty impressive!
What about nominal pressure?
When using hydrogen as a fuel, the main problem is that it must be stored in large quantities since it has a relatively low energy density. This means using a lot of volume. But this is not very helpful for applications such as hydrogen-powered vehicles or fueling stations with reduced space.
Therefore, the only way to solve this issue is by increasing the nominal pressure, with some systems reaching over 1000 bar (∼15000 psi). For trucks, the pressure is usually less than for cars.
These are extremely high nominal pressure values, and not every ball valve can handle these. Therefore, it is vital to guarantee that the valve can work at the expected nominal pressure. This is generally obtained by testing and certifying the valve’s capabilities according to corresponding standards and designing a robust valve with zero leakage.
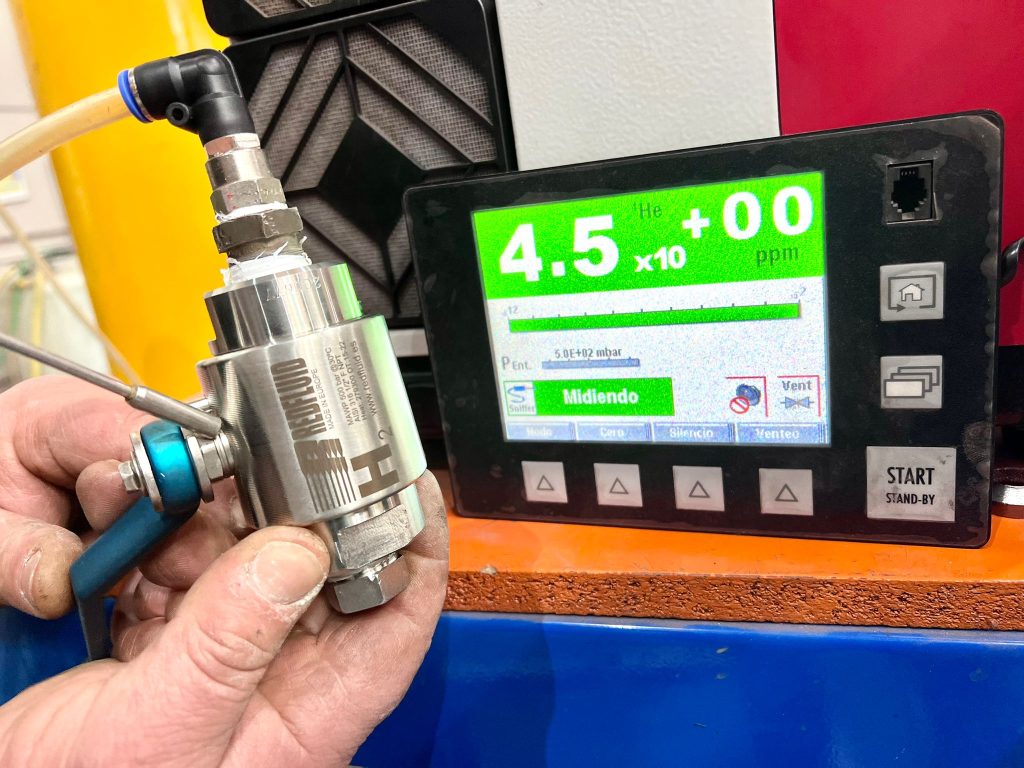
Materials combability
Another critical aspect to consider is the compatibility of the materials used for each component, including seats, gaskets, balls, and bodies. The material selection shall be determined to be acceptable in hydrogen service.
It is essential to consider that some applications will use hydrogen in its gaseous form while others will use it as a liquid. Also, different materials can stand different pressures and temperatures, so an integrated, holistic engineering approach is required.
In terms of materials, there is the standard ISO 15916 Safety of Hydrogen Systems suggests Stainless Steel 316/L as suitable for hydrogen, so the valve metal components (body and ball) could be in 316/L. The non-metal parts (for example, seats) classifies Teflon (PTFE) as adequate. The main issue becomes when high pressure or low temperature is required since the standard does not mention these parameters. In the event of high pressure, PTFE usually is not used as a seat. In that case, the compatibility needs to be double-checked, considering the influence of temperature, fluid, number of cycles, operation, location, and pressure simultaneously.
Test and design standards
Another essential aspect to consider is whether the ball valve has been tested according to the corresponding standard for the specific application. This is important because testing is usually performed to guarantee no leakage occurs and to guarantee good valve performance when used after many cycles.
While leakage is not desired in any system, avoiding it in a hydrogen system is vital as significant hydrogen leakage can lead to fire or even explosions.
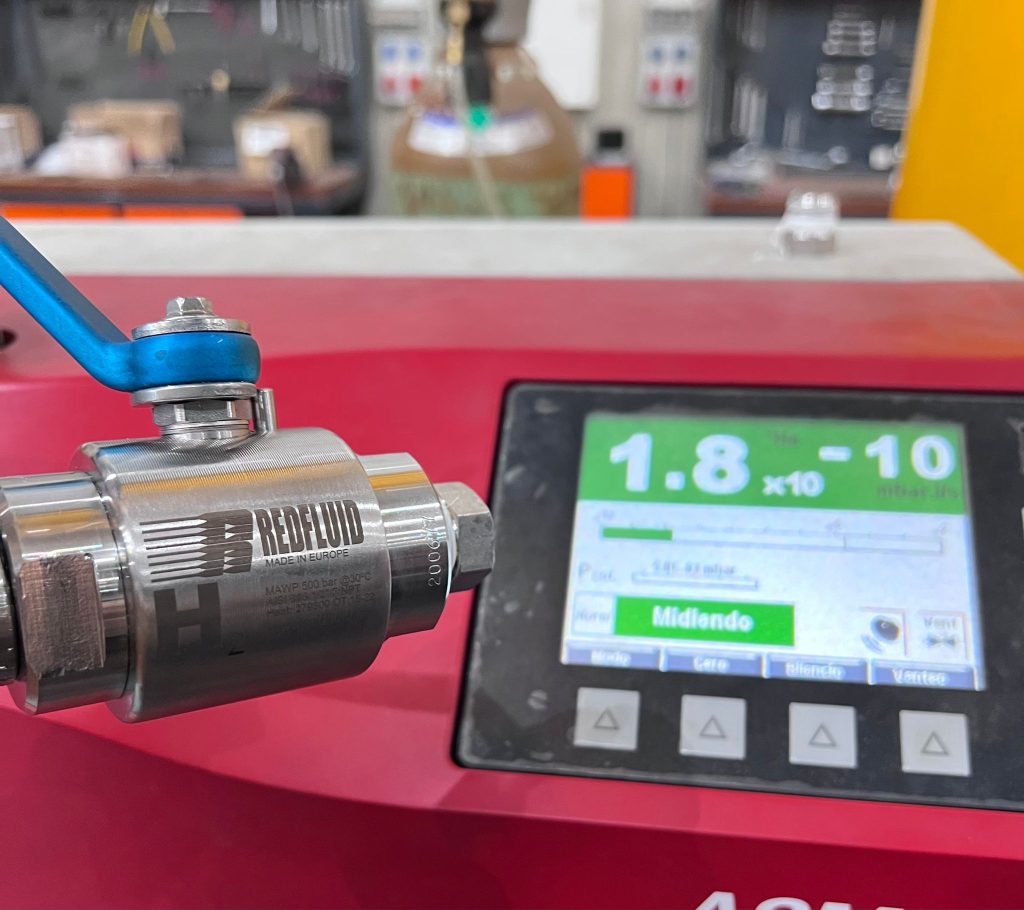
Ball valves are usually leak tested with helium as a medium since it is a gas with tiny molecules. If helium is adequately contained, other fluids will also be contained.
But depending on the application, specific testing may be required to guarantee the proper operation of the valve. It is different if the valve will be installed in the low-pressure hydrogen line than the high-pressure one or if the hydrogen will be liquid or gas.
Testing required for ball valves used for hydrogen systems may include:
- valve inspection and testing based on API 598 or API6D
- fugitive emissions test according to ISO 15848
- metallic valves testing according to EN 12266-1
- pressure testing of metallic valves according to ISO 5208
- inspection and testing of valves for cryogenic service according to BS 6364
- inspection and testing of valve suitable for gaseous hydrogen fueling stations according to ISO 19880-3
Changes that might lie ahead
The future of hydrogen seems to be a bright one, being an excellent alternative for powering many applications, especially in the transportation sector. However, there are still some improvements to make in the technology required to produce hydrogen systems, and their components work as expected and become fully green and mature. For ball valves, this means finding materials that are better suited and improving designs and tests to avoid safety hazards.
Fortunately, strides are being made to achieve the desired improvements. When writing this article, many standards are in development like ISO/CD 19880-6 for Fittings, and the ISO 15916 “Safety of Hydrogen Systems” is being revised.
Consider this before saying that a ball valve is 100 percent suitable for hydrogen; you may need to ask several questions before giving a direct answer. It depends on the pressure, temperature, installation location, hydrogen liquid or gas, standardization, et cetera.
Furthermore, new ball valve types will need to fulfill the requirements and challenging tests as further standardization emerges. The truth is that the future of hydrogen as a source/carrier of renewable energy will bring significant developments in both valve and piping technology, which means excellent opportunities for valve and piping businesses.
Hopefully, you have understood the importance of hydrogen cause we have. But, if you still have questions or you need anything else that is or is not related to hydrogen, don’t doubt to contact us.
2 Responses