Haven’t you heard?
Being sustainable is in!
The world is transitioning to a cleaner, more sustainable energy source, and hydrogen is becoming a candidate for decarbonization.
At Redfluid, we believe in the future of hydrogen and its ability to improve the world. That’s why we have dedicated ourselves to designing a line of valves specifically designed for safe, high-quality hydrogen equipment.
Read on, it’s worth it.
ISO 19880-3: The standard to test for hydrogen valves
Let’s start with technicalities. No worries, I’ll explain it in an easy way.
What is ISO 19880-3 and what is it for?
ISO 19880-3 is an international standard that defines requirements and test methods for valves used in hydrogen fuel systems. The standard covers various aspects of valve performance, including safety, reliability, and durability. These standards are crucial to ensure safety and are recognized by customers worldwide.
Not only must this standard be taken into account when manufacturing a valve, but many other codes and regulations that together create holistic engineering that is integrated into the final design of a valve.
- ASME B31.12 Code (Hydrogen Piping and Pipelines)
- European Regulations how EC79 and EC406 2010 and replaced by regulation (EU) 2019/2144 (Document 32019R2144).
- European Pressure Equipment Directive PED 2014/68/EU.
- European Atex (Ex) Directive for equipment in potentially explosive installations (2014/34/EU).
- Guide to U.S. National Standards for Hydrogen Safety and Hydrogen Systems
Other ISO 19880-3 standards
But in terms of materials that make up the valve, there is a myriad of regulations, standards, and codes for the selection of materials to be compatible with hydrogen, such as ISO 15916. Basic safety considerations for hydrogen systems. This part is complex since all the elements that make up a valve, polymers, elastomers, metallic elements, and even greases and lubricants must be considered.
In addition, other standards that are often applicable to hydrogen valves must be taken into account. Clear examples are Fire Safe (API 607), Fugitive Emissions (ISO 15848), SIL, Cylinder Transport (11114-4)TPED etc.
And logically we cannot abandon the traditional valve testing standards of our industry. API 598, ISO 5208 or ISO 5211, EN 12266-1, the famous B16.34, and a long etcetera.
Manufacture of high-pressure valves for hydrogen
Let’s get down to business.
In order to qualify a valve according to ISO 19880-3, our valves undergo a series of very rigorous tests. These tests are designed to simulate extreme conditions and evaluate the performance of our valves in various scenarios. ISO 19880-3 is a type test, i.e. a test that qualifies a valve design. It is not a production test, i.e. a test that is performed specifically on the valve that is delivered to the customer and will be installed in the plant. In fact, some ISO 19880-3 tests are destructive.
It is important to note that the standard has a section for manual ball valves, and actuated ball valves, but not for needle valves. So the standard itself already indicates that in these cases it should be considered as a miscellaneous valve.
Before testing the valve, the operating conditions of the valve must be defined. That is to say, minimum working temperature, maximum working temperature and maximum working pressure as well as which connection and diameters are required.
The tests to be performed on the valves are as follows:
Example of tests we perform at Redfluid according to ISO 19880-3:
Hydrogen gas pressure cycling test: This test simulates repeated opening and closing of the valve in a hydrogen environment. The objective is to ensure that the valve can withstand more than 102,000 cycles without leakage.
Leak test: This test evaluates the valve’s ability to prevent leakage under various conditions. The valve is subjected to pressure and temperature changes to simulate real-world scenarios.
Worst Case Failure Cycle Test: This test simulates the worst-case scenario in which the valve closes under pressure. The objective is to ensure that the valve does not leak under these conditions.
Proof pressure test: This test applies pressure to the valve to evaluate its capacity. It prevents leakage at 1.5 times the rated pressure (PN x 1.5).
Hydrostatic endurance test: this test applies pressure to the valve to evaluate its ability to withstand high pressures.
Excessive torque withstands test: This test evaluates the valve’s ability to withstand excessive torque. It may cause leakage or damage to the valve connections.
Bending moment test: this test evaluates the valve’s ability to withstand the forces applied to it when connected to a pipeline.
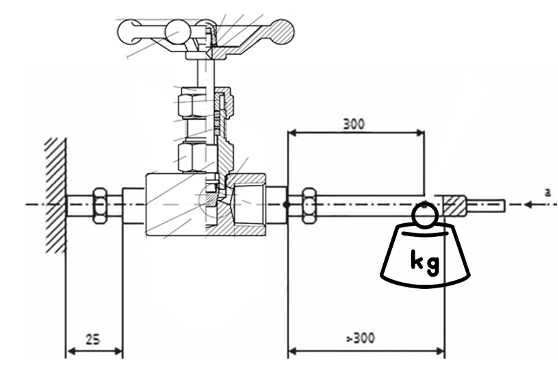
Non-metallic materials test: this test evaluates the performance of the non-metallic materials used in the valve under sudden pressure changes.
Redfluid valves according to ISO 19880-3
At Redfluid, we are proud to be at the forefront of the hydrogen revolution and have our own fully equipped laboratory and facilities to perform these and many, many other tests on our valves. Our commitment to safety, quality, and sustainability is reflected in our products and services. We believe that hydrogen has the potential to change the world for the better. We are dedicated to playing our part in making this vision a reality.
If you are interested in purchasing needle or ball valves for hydrogen or would like more information about our products, please do not hesitate to contact us. We will be happy to answer any questions you may have.
In conclusion, the achievement of ISO 19880-3 qualification for our hydrogen needle valves shows commitment to safety and quality. We are confident that our products will provide reliable and safe performance.
Hey!
And don’t miss out on the latest hydrogen news by following us on LinkedIn. I’ve been a lot on LinkedIn lately, so don’t miss it.