It is no secret that oxygen equipment must be clean and grease and dirt-free.
Cleaning is not only necessary in your home. That goes without saying. It also applies to oxygen equipment.
Be aware that this applies to everyone.
This helps the equipment perform better and ensures that your oxygen flow is safe and free of contamination to prevent possible explosions or accidents.
According to these standards and good practices, let’s look at the details related to the degreasing of oxygen material.
Oxygen problems with dirt
Oxygen systems can experience fouling problems due to the accumulation of deposits on the inner surfaces of pipes and valves.
The most common cause of dirt accumulation in oxygen systems is water droplets. They can form when mixed with moisture in the air. These droplets can settle on the inside surfaces of pipes and valves, causing a buildup of sediment deposits.
Other causes of dirt accumulation can be:
- Dust
- Oils
- Fats
- Other particulate contaminants
These can also accumulate on the inner and outer surfaces of pipes and valves, reducing oxygen flow and increasing the risk of corrosion.
Another major problem with contaminants such as oils and greases is that they are flammable, and can cause serious fires in oxygen systems.
Flammable oxygen
It is not flammable by itself, but it can function as the primary means of starting a fire.
So be very careful, we don’t want to start fires!
This can be easily understood using the concept of the fire triangle, which explains that a fire occurs when 3 elements combine:
- A fuel, such as the contaminants described above.
- An oxidizer, in this case, oxygen
- An ignition source can be a simple spark.
Why degreasing according to ASTM G93?
The ASTM G93 degreasing standard applies to the cleaning of oxygen equipment. The standard includes a process that uses solvents and special machinery to remove oils and other contaminants from equipment.
Thanks to degreasing according to ASTM G39, equipment accuracy and safe operation can be guaranteed. In addition, compliance with this standard ensures compliance with the acceptance criteria of international cleaning standards including:
- ASTM G93
- ISO 15001
- CGA G-4.1
- EIGA IGC 33-18
- SAE ARP 1176
- MIL-STD-1330D
UV light testing
Ultraviolet light testing is a common process used to detect impurities and defects in systems that require degreasing.
UV light is especially useful for detecting hydrocarbon contamination, as its particles fluoresce at the wavelengths of this type of light.
This allows technicians to identify dust and lint particles of 50 microns or larger, as well as a wide variety of oils and greases.
Our degreasing procedure apart from pre-washing; ultrasonic washing; solvent washing; rinsing and drying also includes a UV light inspection.
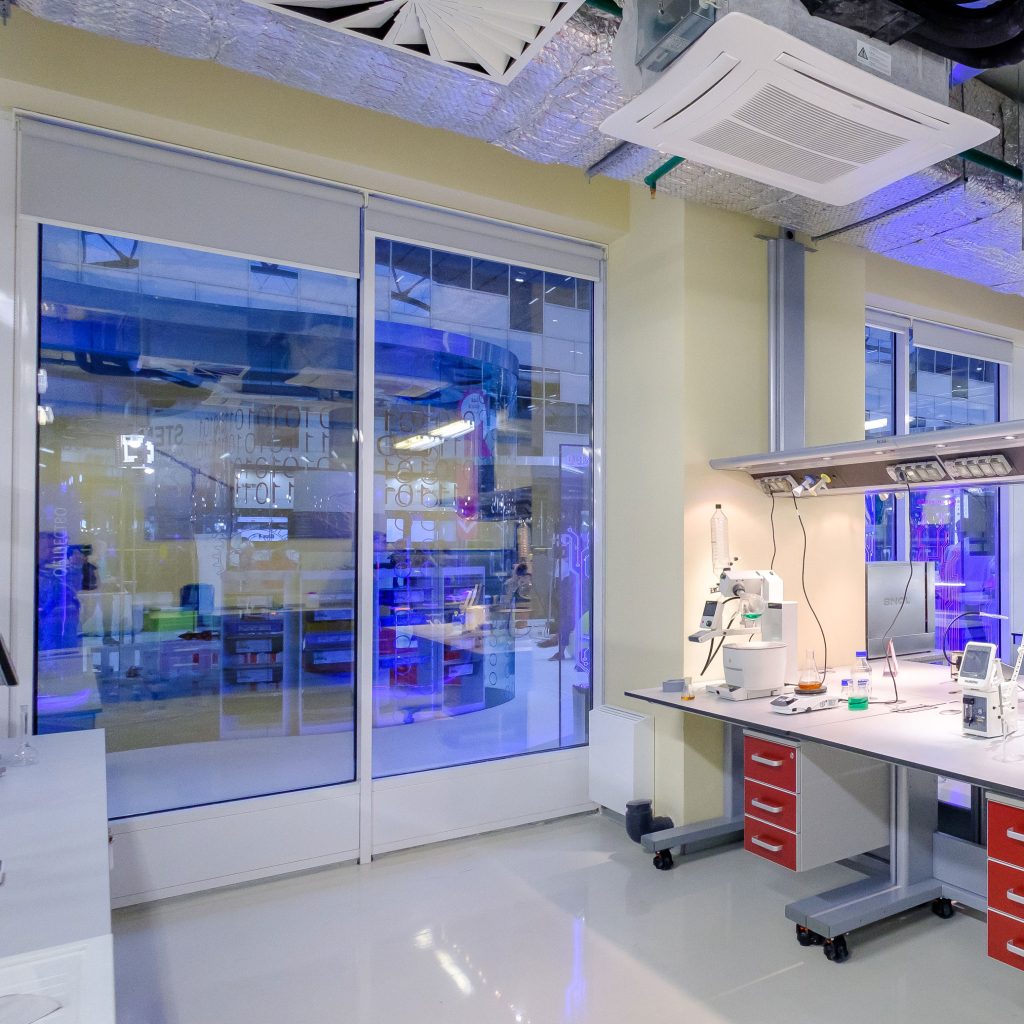
Degreasing certificate
The degreasing certificate verifies that the oxygen degreasing equipment has been properly cleaned and is safe for use in a flow system. The certificate must include the following information.
- Name of the person who has carried out degreasing
- Date of degreasing
- Description of degreasing equipment
- Results of any tests performed on the equipment
At RedFluid we offer oxygen washing service with a degreasing certificate as part of our complementary services.
Sealed unit packaging of oxygen material
Equipment must always be unit packaged and sealed and labeled as clean. Never install or operate material and equipment that is not certified as clean according to the above standards.
Special oxygen-compatible greases
There are a few key points to keep in mind here. First, the grease must be compatible with oxygen, meaning that it does not corrode or degrade in the presence of the material. Also, secondly, the grease must have a high melting point, so that it will not melt at the high temperatures associated with oxygen flow systems. Finally, the grease must be able to withstand the harsh chemical environment present in flow systems.
And don’t forget. You can get in contact with us whenever you need it.