If you think that measurement and control instrumentation are only valves, transmitters, and pressure gauges… then you are wrong. We must consider the small companion, faithful friend of all these instruments: the instrumentation manifold.
Although we usually don’t talk about much in the instrumentation processes, the manifold is one of the essential parts of a process network system. It is responsible for equalizing pressures, handling differential pressures, isolating pressure gauges, purging process piping, blocking or calibrating different lines, and ensuring that everything runs smoothly when measuring in each process. Do you want to know how it works?
Let’s get down to business.
What is the Instrumentation Manifold?
The first thing you should know is that instrumentation manifolds are a type of block-shaped connection system designed to operate at high temperatures and pressures. It can provide isolation, venting, and equalization for various pressure measurement applications inflow or service stations. Manifolds are typically connected to other instruments such as transmitters, pressure gauges, or additional flow rate and pressure sensing devices.
The manifold consists of sufficient piping, valves, and flow controls to collect the produced fluids adequately. It even protects your equipment from excess pressure and temperature! In some cases, it also fulfills the role of distributing injected fluids such as gas or water.
It is handy for pressure instruments that perform measurements in process instrumentation lines.
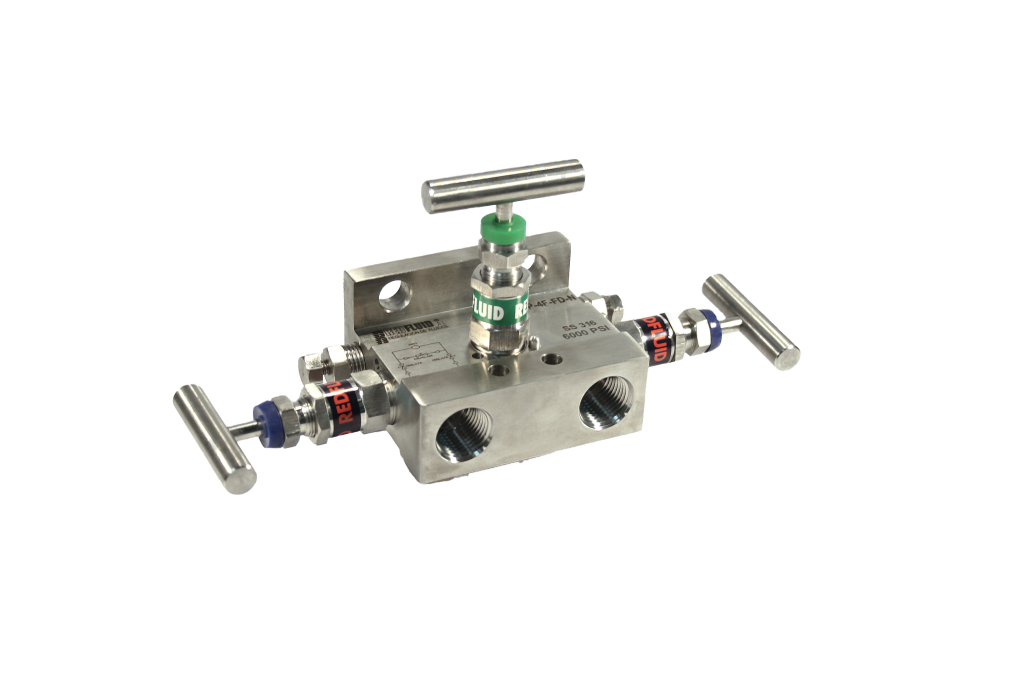
What is the primary function of an instrumentation manifold?
I’ll make you one of those little lists that you can read in a moment. Here you have the functions of a manifold:
- Reduced pressure loss between valves (upstream and downstream).
- Provides an interface between the production pipeline, the flow line, and the process line. Thus, it offers alternatives for multiple tasks.
- Provides a safe and convenient method for isolating, blocking, relieving, and calibrating instruments, gauges, and pressure transmitters.
- Pressure isolation and equalization.
- Differential measurement of liquids and flow control.
- Reduced cost and time for maintenance and installation of equipment.
- Because of its versatility, it is helpful to customize process lines.
- Can isolate an instrument from the process.
- On-site calibration
- Connection of more than two valves for confined spaces.
- Instrument calibration without shutting down the process
Different types of manifold: 1-way, 2-way, 3-way, and 5-valve manifolds
Waaaaait!
Let’s get something straight!
It is sooooo important that you know and understand the difference between the existing range:
Block and bleed manifolds
These are mainly used for absolute and gauge pressure applications and is connected to the process via Male or Female NPT Connections. The low-pressure port is vented to the atmosphere, and the high-pressure port is connected to the process. It allows a clean outlet with no overpressures in the system. In this type of manifold, one valve provides isolation of the instrument, and the other includes venting, draining, and calibration through the test port.
Conventional Manifolds
These manifolds are the most common. They are typically used when we need to install a measuring point on the flange side of the process. We use this type of instrument when we do not want to connect directly to the pressure transmitter sensor. Conventional manifolds are available in 2-way, 3-way, or 5-way models.
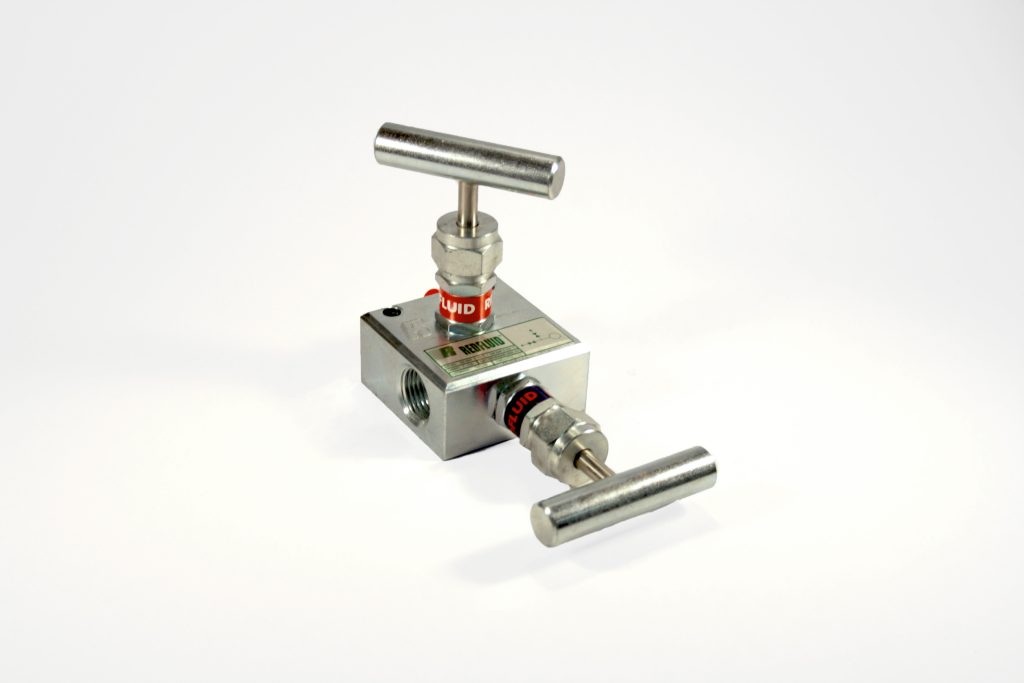
What is a 2-way Manifold?
Two-way manifolds are used for absolute, gauge, and high gauge pressure applications. One valve would provide instrument isolation, and the other would allow calibration of the vent drain through the test port. It prevents the measuring instrument from being loaded and giving erroneous readings. These valves are a barrier between the pressure line and the instrumentation equipment. The second valve provides a vent connection to prevent the line pressure from blocking the instrumentation and a calibration connection.
What is a 3-way Manifold?
Another valve is added to this type of instrument, the equalizing valve. It is useful when equalizing and calibrating the pressure in the line to the transmitter. This can happen if it is disassembled and does not affect the reading. This type of manifold can be used to connect the impulse lines of the system and the transmitters. In this way, it will not affect and will not give errors when applying the control or measurement.
How to use a 3-way Manifold?
The three-way manifold is composed of two block valves and an equalizing valve. If we need to check the zero of the differential pressure transmitter, we have to close the block valve and open the equalizing valve. In this way, we level the system pressure.
What is a 4-way Manifold?
The four-way manifold is used when direct mounting of the differential pressure transmitter is required. These valves contain two mainline block valves, a single vent valve, and a single equalizing valve configuration.
Instrumentation manifolds are an assembly of several valves mounted in a single block with various connections. They isolate a process pipe to an instrument, equalize pressures, and differential pressures, isolate gauges, bleed, block or calibrate different lines.
Number of valves/design
In a single body, instrumentation Manifolds offer a variety of blocking and isolation valves, together with some openings designed for connections to the pipeline using threaded or flanged connections. The number of blocking and isolation valves will be directly related to the Manifold, for which we have:
2-way and 5-way manifold valves
We can use an instrumentation manifold with a 5-way valve for differential pressure transmitters. In addition, they are designed for remote mounting (Ideal for telemetry systems). Due to the dual equalization arrangement (inlet and outlet), this instrument consists of two shut-off valves, two equalizing valves, and a vent/calibration assembly in one assembly, due to the dual equalization arrangement (inlet and outlet). Using this instrument, we can avoid the measurement error due to equalizer leakage between the high and low-pressure connections. For this reason, it is the most suitable for custody transfer applications.
Different applications of a manifold
The application of instrumentation manifolds covers quite a wide range within the industry. From oil and gas through the chemical industry, the power industry, wastewater, metallurgical industry, and especially the pulp and paper industry. Here transmitters and pressure gauges are often used. A short explanation:
Manifolds for pressure transmitters
Manifolds serve a more critical function than you might think. They allow you to shut off or balance the pressure entering the transmitter. This enables your pressure to drop readings to be much more accurate. At the same time, it protects the transmitter (much more expensive equipment) from overpressure in the system.
Manifolds for pressure gauges
Purpose: much more accurate measurement. The purpose of an instrumentation manifold for pressure gauges is to block the process flow in the system so that the process media (upstream and downstream) can be isolated from the instrumentation. It also serves as a block valve to purge or isolate the process media.
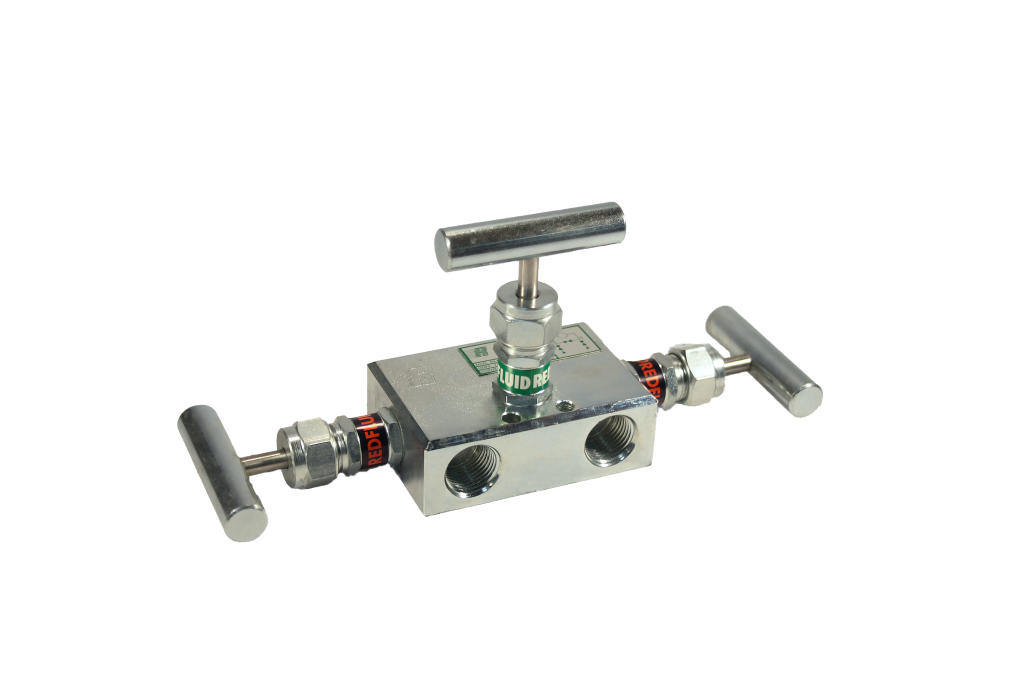
Manifold Threads and Connections
We have heard in many cases the types of connections that exist for an instrumentation manifold, but here is the following question:
What is NPT or NPS, and why is it the type of threads or connections used for a manifold? What is the difference?
Both NPT (National Pipe Threat) and NPS (National Pipe Straight) have the same thread angle, shape, and thread pitch per inch (unit of measurement for establishing thread plies per inch). However, NPT threads are used for instrumentation manifolds because they are tapered and offer better sealing quality. NPS threads are straight and do not offer as much security against leakage.
Instrumentation Manifolds
Here it is essential to highlight the instrumentation manifold with an NPT connection. Unlike the others, it uses its thread to provide a seal since, during assembly, the progressively larger diameter threads in the connection are compressed so that there is no space between the crest and the roots of the rock, which allows forming a complete metal-to-metal seal.
However, good practice indicates that steeply angled rocks are significant within the pipeline, so it is required that thread sealant or tape be applied to the threads to complete a good seal. In some cases, an O-ring will be needed to create a completely airtight seal. Remember that process metering lines should not leak at all!
Instrument Manifold Materials
For the assembly and connection of each of the instrumentation Manifold, components are used according to the ASTM Standard. They can be mainly made of stainless steel 316/316L (stainless steel properties) or carbon steel in both internal and external components. However, they can also be built depending on their application for corrosive areas, high pressure, or high temperatures.
If you want to know more about the world of instrumentation and control, we recommend you to read our post: “What is the difference between ball and needle valves?” And if you have any questions, do not hesitate to contact us.