Needle valves are very important elements in a piping system, so it is essential to understand the difference between butt weld and socket weld in needle valves to get them correctly installed. As it would happen with any other valve, a needle valve that is not properly installed would not serve its main purpose, controlling flow.
If you are interested in learning about butt weld and socket weld and how they affect needle valves installation, keep reading as we explain everything you need to know about it.
In case you have some Spanish knowledge, I leave you a video that speaks about the topic in only 5 minutes.
What is Butt Weld?
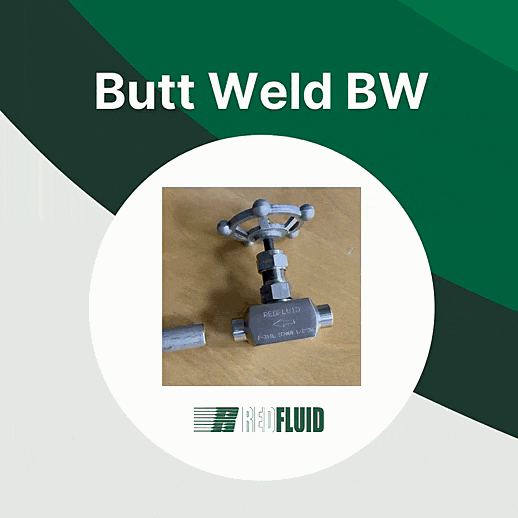
Butt weld or BW is the name given to the welding method that consists in taking the ends of pipes or the end of a pipe and a fitting, putting them one against the other (face to face), and performing the welding around their diameter while keeping the pressure to avoid displacement of the faces.
Of course, there will be times when butt weld is the best alternative, but others where the method should be discarded. Let us illustrate the previous statement by sharing the pros and cons of butt weld.
Advantages of Butt Weld (BW)
- High strength and stress resistance which makes it suitable for high operation pressures.
- Suitable for large diameters and small diameters with high wall thickness.
- Suitable for different materials.
Disadvantages of Butt Weld (BW)
- It requires a higher level of welding skills to be performed.
- It requires beveling the ends for proper weld penetration.
What is a Socket Weld?
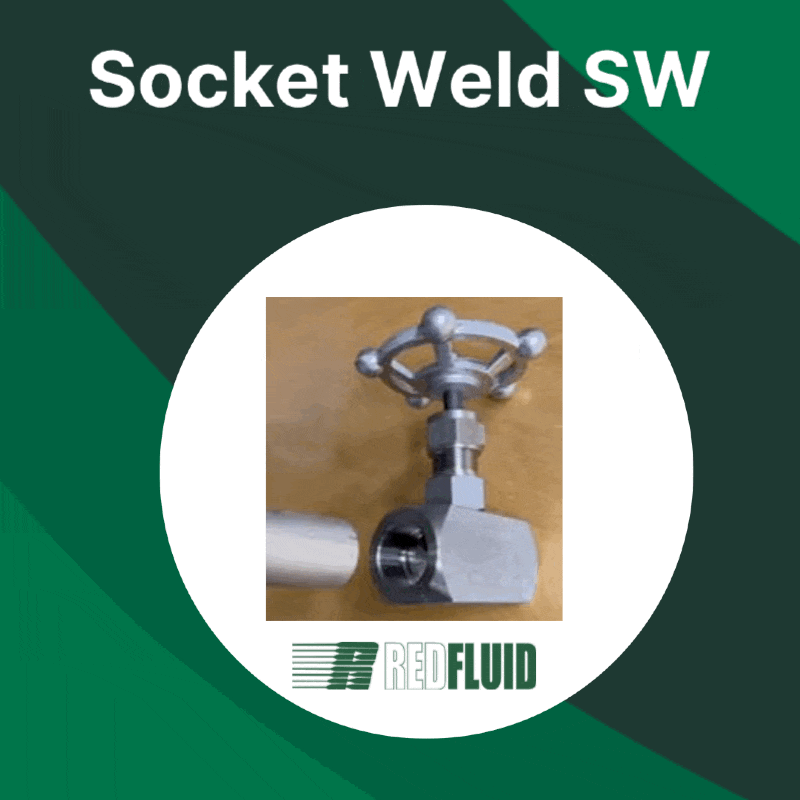
Socket weld or SW is another welding method for pipes and fittings. This method requires one of the pieces being welded to be smaller in diameter than the other so it can be placed inside, hence the name. Then the welding is created around the outside circumference of the larger diameter.
Let’s see know the pros and cons of this type of weld.
Advantages of Socket Weld (SW)
- It requires fillet welding which is easy to achieve.
- Especially suitable for small diameters working at relatively high pressures.
- No preparation required other than cleaning the surfaces.
- Suitable for different materials.
Disadvantages of Socket Weld (SW)
- Strength and stress resistance is reduced due to limited weld penetration in the fillet.
- Not suitable for systems with fluids sensitive to contamination or reaction with the welding.
Butt Weld (BW) and Socket Weld (SW) Standards
Both welding methods are regulated by ANSI/ASME standards. For Butt Weld, the ANSI B16.25 standard applies, and for Socket Weld the standard is ANSI B16.11.
According to ASME, the B16.25 standard “covers the preparation of buttwelding ends of piping components to be joined into a piping system by welding. It includes requirements for welding bevels, for external and internal shaping of heavy-wall components, and for preparation of internal ends, including dimensions and tolerances. Coverage includes preparation for joints with the following: no backing rings; split or noncontinuous backing rings; solid or continuous backing rings; consumable insert rings; gas tungsten arc welding (GTAW) of the root pass.”
For the B16.11 standard, they claim that it “covers ratings, dimensions, tolerances, marking and material requirements for socket-welding and threaded forged fittings. These fittings are designated as Class 2000, 3000, and 6000 for threaded end fittings and Class 3000, 6000, and 9000 for socket-weld end fittings.”
These standards are recommended as their users will be capable of complying with regulations while achieving the operational, cost, and safety benefits to be gained from the many industry best practices they describe in detail.
What are the differences of using BW and SW in needle valves?
So far, we have described both butt and socket welding methods in general terms. Now, how do their characteristics, advantages, and disadvantages apply to needle valves?
Well, probably the main difference you will see between BW and SW in needle valves is the range of diameters they cover. Butt weld works for both small and large diameters, usually DN50 and above, but SW only works properly for those in the range of DN100 or below.
For example, our Serie 3.000 needle valve with BW connection is offered for 11 diameter sizes, while the SW connection can only work for 4 smaller diameters.
Another important aspect to consider is the strength of the weld. While socket weld can be strong enough for many applications, butt weld provides double the strength which is usually not lower than the strength of the welded material.
Also, socket weld is definitely easier to install. However, due to the thermal expansion that may happen while welding and during operation, a gap of 1/16″ approximately is usually required at the bottom of the pipe the valve will socket into. The problem is the possibility of excessive stress that may result in cracks in the weld. So, this is why butt weld is usually a more durable connection for needle valves, although it is more difficult to achieve as it requires more time and a highly trained and experienced welder.
Another problem would be using socket weld connections with corrosive fluids. Due to the discontinuity of the smooth pipe internals crevice corrosion may appear and the weld may fail.
Last but not least, there is the price. While socket weld connections are usually more expensive than butt weld connections for the needle valves, the installation of butt-welded needle valves can be much more expensive due to labor times and costs.
Of course, some of these issues can be mitigated. For example, by using 321 steel which is similar to SS 304 but with a titanium addition of at least five times the carbon content, we have been able to reduce carbide precipitation during welding for our high-temperature needle valve. This makes the connection stronger and more durable.
How to select the right connection for my application?
At this point, you should have the difference between butt weld and socket weld in needle valves clear. However, you may be wondering whether you are using this information correctly to choose the type of connection for your needle valve. Let us help you.
In summary, the main considerations are:
- Piping diameters in your system.
- Type of fluid in the system.
- Wall thickness to determine whether beveling is possible or not.
- Operating pressures.
- Operating temperatures.
Of course, there may be situations when the best option is difficult to identify. So, whenever in doubt, the recommendation is to contact the experts in the field.
Fortunately, we offer a wide variety of needle valves for different operating pressures ranging from 255 bar to 700 bar. Some of them can also work at very high temperatures in the 800° Celsius range and also cryogenic ones.
If you are having trouble finding the best valve for your specific application, or you would like more about the different valves we have in stock, do not hesitate to contact us and we will be more than happy to help you.
One Response