Let’s see. First of all, it is necessary to make a sketch of what we are talking about. We have different names for condensate pot and synonyms for the same part, but with different functions. Some distribute air or fluid and others are used to separate or condense steam.
Here is a short list to give you an idea:
- Barrel
- Bottle rack
- Condensate chamber
- Cylinder
- Manifold
- Condensate Collector
- Condenser
- Condensate receiver
- Separation tank
- Distributor
- Manifold
- Condensate pot
- Separation pot
- Sampling
I have already told you that there are many names to describe the same thing.
Many of these names are used interchangeably in the industry, but they can be classified into two main groups.
Let’s get into the first group:
Condensate pots
Condensate pots are pressure vessels designed to capture and retain condensate and any particles or foreign bodies that may accumulate in gas system piping. The pots allow instruments and valves to be connected directly to the pipeline for sampling purposes, as the pot provides a secure barrier between instruments and steam or gases present in the pipeline.
In addition, the condensate pots are also used for:
- High temperature prevention
- Impurity prevention
- Improved instrument readings
Let’s dig a little deeper into the group of condensing pots.
Condensate pots in steam systems
In steam applications, condensate pots are crucial to protect pressure transmitters and ensure accurate measurements. These vessels condense the steam before it reaches the instruments. They are strategically installed where they collect condensate liquids and through a purge are collected inside. The steam or air continues to flow through the piping.
The separation pot in steam systems
Similar to the condensate pot, but used specifically for measuring the flow of corrosive and high density fluids. It is filled with a liquid that does not mix with the process fluid, providing an effective barrier that protects the instruments and ensures pressure transmission without direct contact with the problematic fluid.
Collectors or distributors
This is the large group number 2. And be very careful with this. You can’t confuse it with instrumentation manifolds. The collectors are a series of outputs and inputs connected to a circuit. Sometimes, they can have various sizes and different types of connections to accommodate all process needs.
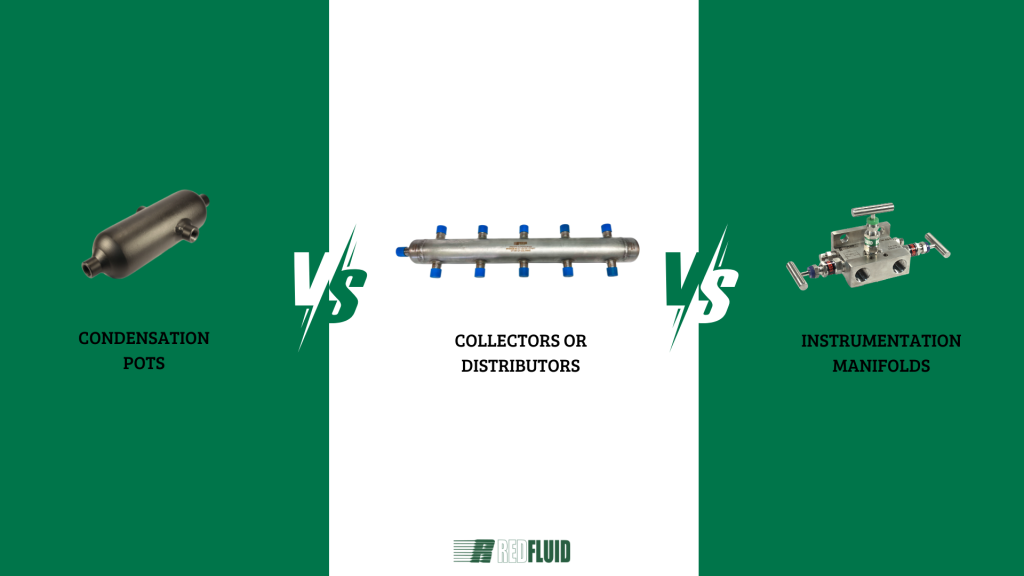
What to consider when ordering a Condensate Barrel, Distributor, or Condensate Pots
This part is almost the most important. When we are asked for barrels, some information is always missing. Whether it is the thickness, the number of entries, the dimensions… For this reason, I leave you a list of what you have to take into account when you ask us for a distributor.
- Volume: It is the capacity of the cylinder, normally in Liters. The larger the volume, usually the greater the condensate capacity. A larger pot extends the residence time of the gas flow, improving condensate droplet separation due to longer settling time. The larger cross section will reduce the gas flow velocity somewhat and hopefully can lead to easier droplet separation.
- Working pressure: Maximum system pressure.
- Diameter and type of each connection: For each connection (inlet, outlet and purges) we need to know the diameter or DN, and what type of connection: if it is threaded (BSP, NPT …) male or female. If we want connections for welding we need to know if it is SW or Butt Weld.
- Distance between connections: Usually in millimeters it is the distance between each of the lateral connections of the barrel. Other key distances are: total length, length of each connection, etc. They can also be manufactured with special connections such as flanged or with pre-assembled fittings.
- Diameter of the main pipe and wall thickness or Schedule (SCH): It is the diameter of the body of the pot, in general depending on this diameter and thickness we will have a volume or another. The thicker it is, the more pressure the bottle rack will be able to withstand.
- Construction material: It is the material of the product itself, the most common are stainless steel type 316 or carbon steel A106 or A105, but can also be manufactured in other special materials such as superduplex, P22 or P91, monel or nickel alloys.
- Construction regulations: Depending on where the distributor is installed, different regulations such as CE marking PED 2014/68/EU, ASME BPVC or EN design codes, material certificate type EN 10204 3.1 or Welding procedures type WPS; PQR, WPQR must be requested.
- Non-destructive tests: Pressure tests in air (pneumatic), hydrostatic tests in water. Or tests on welds such as Penetrating liquids, Magnetic particles, Visual inspection on welds, X-rays performed by approved personnel.
In short, understanding the function and variety of condensate pots, manifolds and manifolds is essential to optimizing the performance of any steam system or corrosive and dense fluid handling system. From selecting the right volume and working pressure, to choosing the right material of construction and connections, every detail counts to ensure the efficiency and safety of your installation. At Redfluid, we are committed to providing you with high-quality, customized solutions tailored to your specific needs.
Hey, and don’t hesitate to contact us with any questions or specifications; our team of experts is ready to help you choose the best equipment for your project. Together, we can make your operations safer, more efficient and reliable.