This article is short but intense. Very attentive to everything. I am going to explain to you in the best possible way what a check valve is.
Check valves are essential components in high-pressure pipelines. The function of a non-return valve is to allow the fluid to flow in one direction and prevent it from flowing in the other. It avoids damaging the instruments of your installation or mixing different fluids.
Its operation is based on the creation of an opening pressure (cracking pressure) higher than the static pressure of the system.
For the check valve to close without any leakage, the inlet and outlet sides need a pressure differential between them, known as resealing pressure. The resealing pressure usually requires back pressure. It is needed to ensure that the valve closes tightly.
The function of the non-return valve
The check valve can be compared to an emergency door in a discotheque. It can be opened from the inside, but from the outside, it does not let anyone in. In this case, a one-way valve allows flow in one direction but not in the opposite direction to the arrow.
Additionally, in the direction of the arrow, it closes hermetically until a minimum pressure in the pipeline is not exceeded. Check valves or one-way valves are ideal for preventing fluid backflow in high-pressure pipelines.
As you know, check valves are an essential part of any system operating at high pressures, but it is also important that the system pressure remains stable. That is why the use of check valves or non-return valves capable of preventing the system from being unprimed is of vital importance to ensure its correct operation.
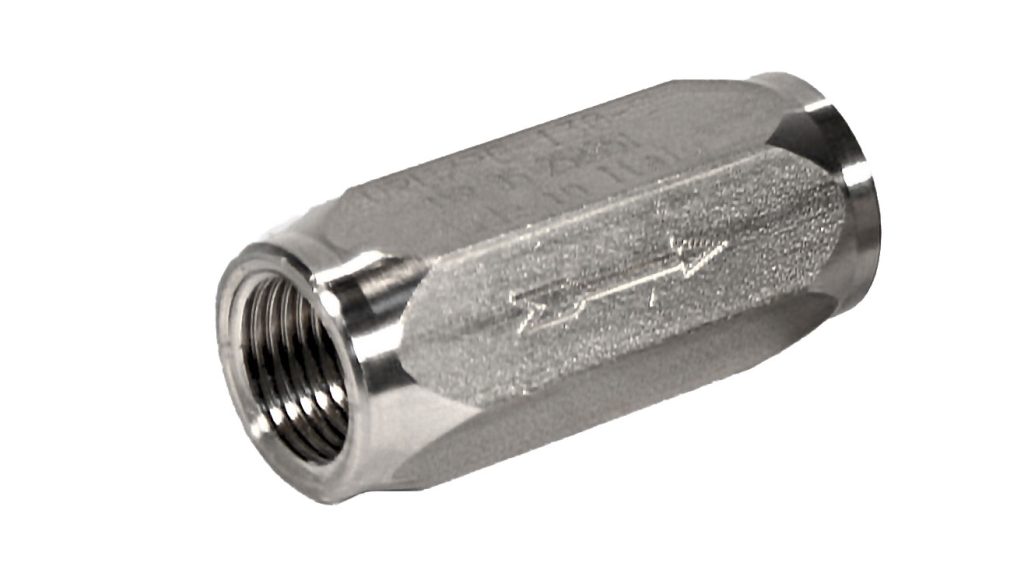
Definition of cracking pressure in a check valve
In high-pressure systems, a check valve can be opened and closed many times a day. Each time the valve opens, fluid is about to flow backward through the valve, but the spring in the valve keeps the disc or piston closed. It is this spring force that is known as cracking pressure. Cracking pressure is not necessary once the check valve is already open.
Cracking pressure is the pressure required for a check valve to open. It occurs when the fluid exerts a force on the valve that exceeds the force of the closing spring. Normally a check valve has a cracking pressure of about 0.5 bar. It can vary greatly depending on each manufacturer or type of spring.
Sometimes also called burst pressure and explained in other words it would be the pressure that allows the valve to open when it exceeds the spring torque and any downstream pressure acting on the back of the disc or piston. On initial opening and start-up, an upstream pressure is applied to the inlet side of the valve.
The pressure differential between upstream and downstream where the valve opens is called the burst pressure. When the pressure differential exceeds the burst pressure, the valve piston “opens” and allows the fluid to flow.
Important! A check valve is not a safety valve! It should not be used as the main valve in a safety-critical system.
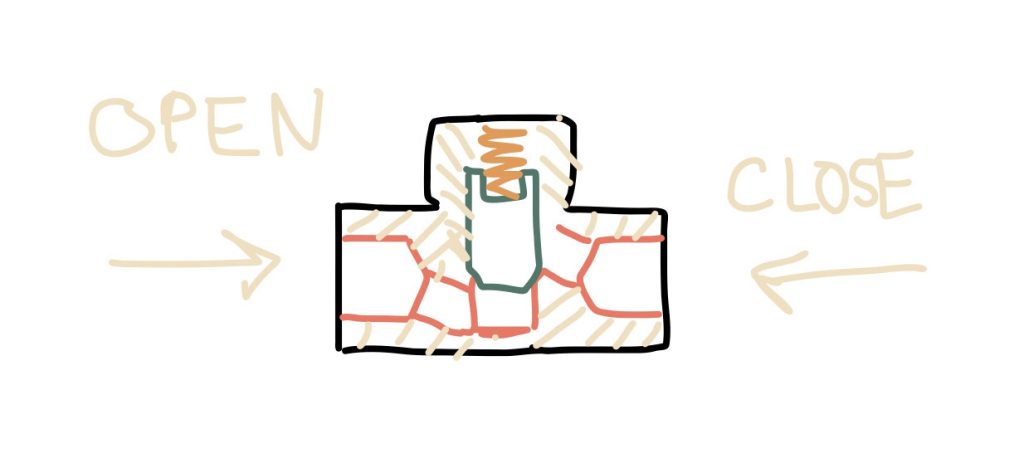
Typical problems with check valves
These valves may present some problems, of which the most typical are:
- The valve spring may fail, causing the valve to open accidentally.
- Dirt or particles of different materials can clog the valve seat, causing it to close tightly.
- Corrosion can damage the metal parts of the valve, which would cause it to open or close unexpectedly.
To avoid these problems, it is important to follow a series of maintenance steps, such as:
- Periodically clean the valve seat to remove accumulated dirt.
- Replace the valve spring and gaskets when they are becoming damaged.
- Periodically inspect check valves for any problems.
In this way, you will be able to keep the check valve in good condition by performing a periodic check. In any case, if you detect any of these problems, it is important to have the valve checked by a professional and, if necessary, repaired or replaced.