Understanding this difference is a must. I have been asked a thousand times what the difference between tubing and piping is. Although it may seem the same, it is not. Come on take some notes.
Let’s get down to business.
In our industry, tubing refers to any pipe, whether of a circular cross-section, which is measured by its outside diameter (OD) and wall thickness (WT).
On the other hand, piping refers only to circular tubular pieces used for fluid distribution, which are designated according to their nominal size (NPS or DN), the designation used to indicate the capacity of the piece. When we talk about Pipe, we usually refer to ASME B36.10M/19M-2018 standard sizes.
¡Hey, hey, hey! Wait a minute.
Difference between tubing and piping with video (easy)
I have already said that this blog includes a cool video. In it, I explain the whole thing in 3 minutes. I leave it here so you can take a look at it. (The video is in Spanish, but this way you get to know me a bit).
For this blog, I also wanted to leave you a pdf file about tubing and pipe (since the video is in Spanish). I felt very inspired this time.
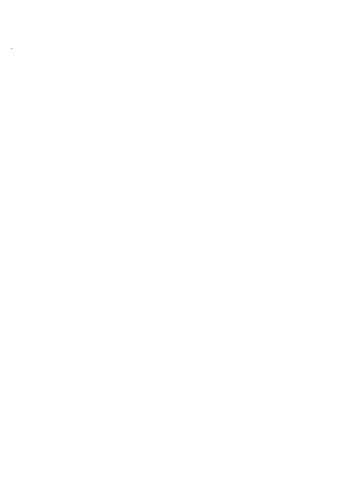
If you want the pdf file you only have to press the button and you are ready to go.
OD instrumentation tubing
OD instrumentation tubing is related to circular cross-section tubes, so they are measured according to their outside diameter. They are generally made of materials with special characteristics for their application in instrumentation such as stainless steel, duplex, nickel, or titanium, and their walls are relatively thinner than other types of tubing.
When we talk about a tube we always refer to it by its outside diameter, and normally we add the suffix OD (outside diameter) x its thickness. In the market, we can find tubing in imperial sizes (inches) as well as millimetric (European diameters with millimeters). For example, in the following image, we have a 1/2 “OD x 0.049” tubing and when we measure it with the caliper it is exactly what it gives.
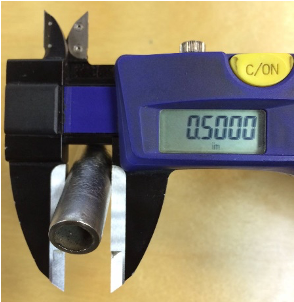
Here are the most common instrumentation tubing sizes:
OD (mm) | Wall Thickness (mm) | OD | Wall Thickness (inch) |
3.17 | x 0.51 | 1/8″ | x 0.020″ |
6.00 | x 1 | | x 0.039″ |
6.35 | x 0.89 | 1/4″ | x 0.035″ |
7.94 | x 0.51 | 5/16″ | x 0.020″ |
8.00 | x 1.00 | | x 0.039″ |
9.52 | x 0.89 | 3/8″ | x 0.035″ |
10.00 | x 1.00 | | x 0.039″ |
12.00 | x 1.00 | | x 0.039″ |
12.70 | x 1.24 | 1/2″ | x 0.048″ |
13.00 | x 1.00 | | x 0.039″ |
14.00 | x 2.00 | | x 0.078″ |
15.00 | x 2.00 | | x 0.078″ |
16.00 | x 2.00 | | x 0.078″ |
18.00 | x 2.00 | | x 0.078″ |
19.05 | x 1.60 | 3/4″ | x 0.06″ |
20.00 | x 1.00 | | x 0.039″ |
22.00 | x 1.00 | | x 0.039″ |
24.00 | x 1.00 | | x 0.039″ |
25.00 | x 1.00 | | x 0.039″ |
25.40 | x 2.11 | 1″ | x 0.083″ |
28.00 | x 2.00 | | x 0.078″ |
30.00 | x 2.5 | | x 0.098″ |
List of tubing standards for instrumentation:
ASTM A-213 | Standard specification for seamless ferritic and austenitic steel tubes for boilers, superheaters, and heat exchangers. |
A-269 | Standard specification for seamless and welded austenitic stainless steel tubes for general services. |
A-789 | Standard specification for seamless and welded ferritic/austenitic stainless steel pipes for general services. |
EN-10216-5 | Seamless steel pipes for pressure applications. Technical delivery conditions. Part 5: Stainless steel tubes. |
EN-10305-1 | Steel tubes for precision applications. Technical delivery conditions. Part 1: Seamless cold-drawn tubes. |
EN ISO 1127 | Stainless steel tubes – Dimensions, tolerances, and conventional masses per unit length. |
DIN 17458 | Seamless austenitic stainless steel circular pipes are subject to special requirements – technical conditions of delivery. But currently suspended by the new DIN EN 10216-5. |
Each of these standards also talks about thickness and internal diameter tolerances. But we will leave this for another blog article.
What is seamless?
As its name suggests, this type of tubing does not have any welding seams, so they are completely smooth, being especially ideal for the precision required in instrumentation. In addition, the absence of these seams ensures reliability by preventing leakage through the seam. In addition, this type is generally stronger and offers greater resistance to high pressures and corrosion. It is the tube we recommend for double-ring or single-ring fittings DIN 2353.
And the other way around – Sewn or welded
This type is usually manufactured from a flat piece that is rolled to achieve the circular cross-section by welding the ends longitudinally to close the cross-section. This is why a seam is generated. The main benefit is that it is less expensive to manufacture, so the selling price is usually lower. However, this type is not recommended for high pressures and corrosive environments.
Before reading on, I remind you that I have a pdf that explains the difference between pipe and tubing on a single page.
Before reading on, I remind you that I have a pdf that explains the difference between pipe and tubing on a single page.
So, if you want it, just hit download.
Pipe (ASME B36.10)
To speak of “ASME B36.10 pipe” is to speak of a seam or seamless forged steel pipes or tubular pieces for high or low temperature and/or pressure applications. The ASME B36.10 standard is responsible for designating the dimensions of such pipes according to their NPS or DN. The NPS designation of the standard allows obtaining through the corresponding table dimensions such as Schedule, Wall Thickness (WT), and Outside Diameter (OD) of the corresponding pipe.
License or Schedule
The scheduled number of a pipe is related to the wall thickness of the pipe. The higher the schedule number, the greater the wall thickness of the pipe. However, there is also the case where two pipes have the same schedule number, but their wall thickness is different. This is due to the size of the pipe. In this case, the larger pipe size will be the one with the greater wall thickness.
The higher the Schedule, the thicker the pipe and the more pressure it will withstand.
Therefore, to define a pipe we must state its nominal diameter (Nominal Pipe Size or DN) and the Schedule value (thickness). At the beginning of the Schedule standard, there were only 3 types: STD (Standard), XS (extra-strong), and XXS (double extra-strong). Over time, SCHs have been added up to the current nomenclature. In the table below we can see that the outside diameter remains constant and depending on the Schedule we will obtain different inside diameters:
NPS | DN | OD (en mm) | SCH 5 | SCH 10s/10 | SCH 30 | SCH 40s/40 STD | SCH 80s/80 XS | SCH 120 | SCH 160 | XXS |
1/8 | 6 | 0.405 (10.29) | 0.035 (0.889) | 0.049 (1.245) | 0.057 (1.448) | 0.068 (1.727) | 0.095 (2.413) | – | – | – |
1/4 | 8 | 0,540 (13.72) | 0.049 (1.245) | 0.065 (1.651) | 0.073 (1.854) | 0.088 (2.235) | 0.119 (3.023) | – | – | – |
3/8 | 10 | 0.675 (17.15) | 0.049 (1.245) | 0.065 (1.651) | 0.073 (1.854) | 0.091 (2.311) | 0.126 (3.200) | – | – | – |
1/2 | 15 | 0.840 (21.34) | 0.065 (1.651) | 0.083 (2.108) | 0.095 (2.413) | 0.109 (2.769) | 0.147 (3.734) | – | 0.188 (4.775) | 0.294 (7.468) |
3/4 | 20 | 1.050 (26.67) | 0.065 (1.651) | 0.083 (2.108) | 0.095 (2.413) | 0.113 (2.870) | 0.154 (3.912) | – | 0.219 (5.563) | 0.308 (7.823) |
1 | 25 | 1.315 (33.40) | 0.065 (1.651) | 0.109 (2.769) | 0.114 (2.896) | 0.133 (3.378) | 0.179 (4.547) | – | 0.250 (6.350) | 0.358 (9.093) |
1 1/4 | 32 | 1.660 (42.16) | 0.065 (1.651) | 0.109 (2.769) | 0.117 (2.972) | 0.140 (3.556) | 0.191 (4.851) | – | 0.250 (6.350) | 0.382 (9.703) |
1 1/2 | 40 | 1.900 (48.26) | 0.065 (1.651) | 0.109 (2.769) | 0.125 (3.175) | 0.145 (3.683) | 0.200 (5.080) | – | 0.281 (7.137) | 0.400 (10.160) |
2 | 50 | 2.375 (60.33) | 0.065 (1.651) | 0.109 (2.769) | 0.125 (3.175) | 0.154 (3.912) | 0.218 (5.537) | 0.250 (6.350) | 0.343 (8.712) | 0.436 (11.074) |
In the figure below we can see a 1/2″ SCH80 nipple TOE. The outside diameter is 21.30 mm. and it has a thickness of 3.74. It matches the table above:
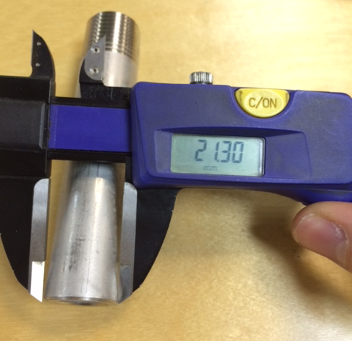
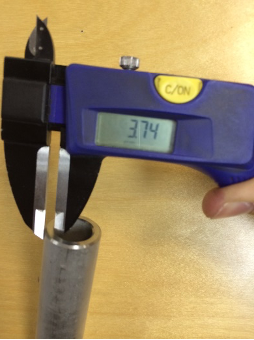
Buuuuuut,
If we convert 21.30 mm to inches we get 0.83″ (1mm= 0.039″) so it is not 0.5 (½”), this is why we ALWAYS have to use a table to make the conversion in piping cases.
List of standards that tell us about these measures DN, NPS and follow this table of measures:
ISO 6708 | Pipework components — Definition and selection of DN (nominal size) |
ASME B36.10M | Welded and Seamless Wrought Steel Pipe |
EN 12516-1 | Industrial valves. Mechanical strength of the enclosure. Part 1: Method of tabulation for steel valve casings. |
Where does the chaos come from? Why so much confusion in understanding the difference between tubing and piping?
Well, once again, it’s about the polysemous word. That is to say that one thing written in the same way has two different meanings.
For example, a customer says: send me 6 meters of 1/2″ stainless steel pipe.
Well, it is already mixed up, it can refer to 1/2″ of tubing and therefore 12.70 mm outside diameter or 1/2″ of piping which is much larger 21.30 mm, look at the difference:
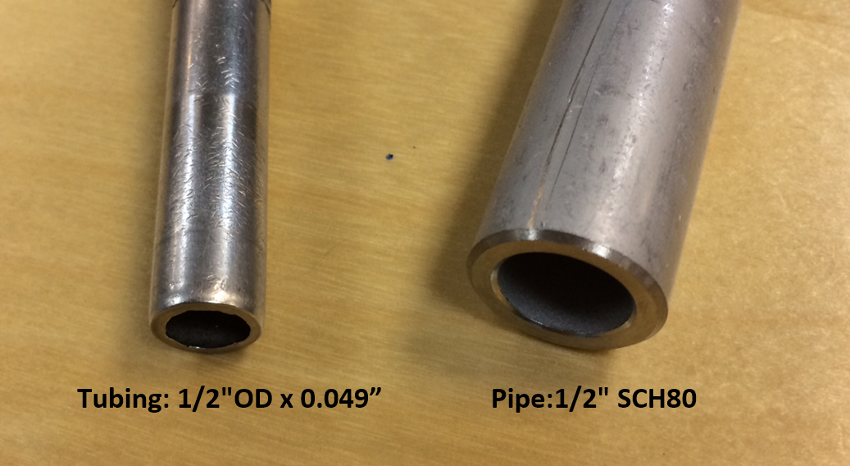
Wall thickness
The wall thickness or WT is the actual value of the wall thickness and is usually expressed in inches or millimeters. As mentioned before, under the same Schedule Number there can be different thicknesses, since it depends on the size of the pipe. The higher the NPS, the greater the thickness.
NPS, DN, OD, ID, SCH when dealing with piping and tubing
These are the most important abbreviations when dealing with tubing and piping:
NPS = Nominal Pipe Size
DN = Diametre Nominel
OD = Outside Diameter
ID = Internal Diameter
SCH = Schedule
Cold Drawn in Spanish estirado en frio
Type of connection (Double ring fittings, DIN2353 or Solder)
Quality instrumentation tubing offers easy connection with other elements such as single-ring compression fittings (DIN 2353), or double-ring fittings without the need for threads and welds, thus increasing accuracy while avoiding possible leaks.
Of course, for pipes according to ASME B36.10, threaded and welded SW or BW fittings are available.
We also have fittings and converter adapters that convert instrumentation tubing sizes to piping sizes.
I hope you now know the difference between piping and tubing, otherwise, download the pdf. And if you still need some help contact us, we’d love to chat with you.